Preservation Periodical: Volume 4, Issue 2
Summer 2025
Concrete Heritage: Restoring the Iconic Walls of the Hirshhorn Sculpture Garden
By Will Davies
The Hirshhorn Museum’s Sculpture Garden, situated within the National Mall in Washington, D.C., is undergoing a significant revitalization. Originally designed by Gordon Bunshaft of Skidmore Owings & Merrill in the 1970s, the Hirshhorn Museum and Sculpture Garden is notable not only for its minimalist aesthetic but also for the use of a distinctive aggregate concrete and sandblasted finish. As part of a broader effort to preserve the historic fabric, correct original construction deficiencies, and enhance the space for modern art, the perimeter concrete walls of the Sculpture Garden are being reconstructed in-kind.
When Bunshaft’s design for the Hirshhorn Sculpture Garden was completed in 1974, his vision was rooted in modernist principles—clean lines, austere forms, and a deliberate use of materials. At the heart of this vision are the Garden’s concrete perimeter walls, cast in place with Swenson Pink granite aggregate, which gave the walls texture, color, and character. These walls served not just as structural boundaries but as standalone aesthetic elements, framing sculptures while reinforcing the quiet, contemplative nature of the space. The perimeter concrete walls are also a fundamental unifying feature of the Hirshhorn campus, consistent with the concrete of the building drum and the Plaza walls.
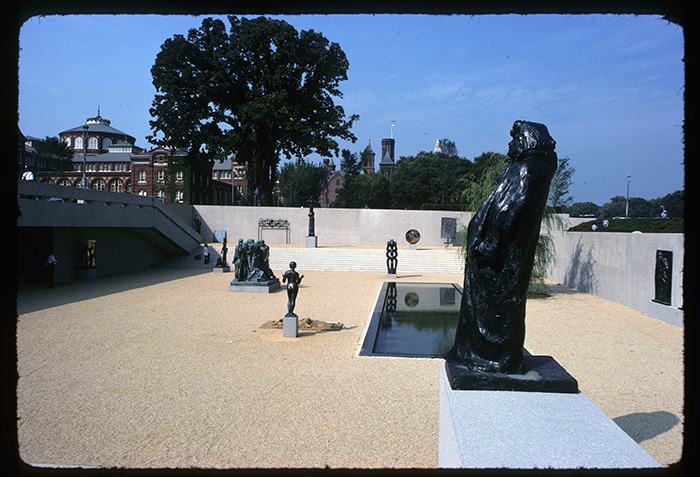
The primary reason for the reconstruction of the existing perimeter walls was the prevalence of alkali-silica reaction (ASR), also known as “concrete disease”, a chemical process that can cause concrete to crack, expand, and fail over time. Signs of deterioration from ASR in the concrete walls included discoloration, extensive visible horizontal cracking, and other indicators of material distress. The original design lacked adequate waterproofing and could not be repaired without a complete replacement of the concrete. Given the previous issues, ASR risk mitigation was crucial for the new concrete. This required specialized concrete mix designs, rigorous testing, and expert oversight.
Preservation standards required that all elements be replaced “in-kind,” meaning materials and finishes had to match the original to the highest degree possible. This commitment to authenticity guided every aspect of the project, from quarrying stone to pouring concrete to finishing surfaces. The original concrete featured Swenson Pink granite, a distinctive aggregate quarried from a small site in Wells, Maine. Known for its subtle pink hues, fine grain, and black gneiss inclusions, Swenson Pink brings a warm, natural tone to the background of the Hirshhorn campus. Within the Sculpture Garden, the granite was used not only in the walls but also in walkways and stairs, making it a unifying element across the campus’ design language. Sourcing the granite was challenging, as the small quarry has long ceased mass production. The quarry substantially increased its operations to produce dimensional stone and aggregate, enabling this project to maintain the exact granite used in the original design.
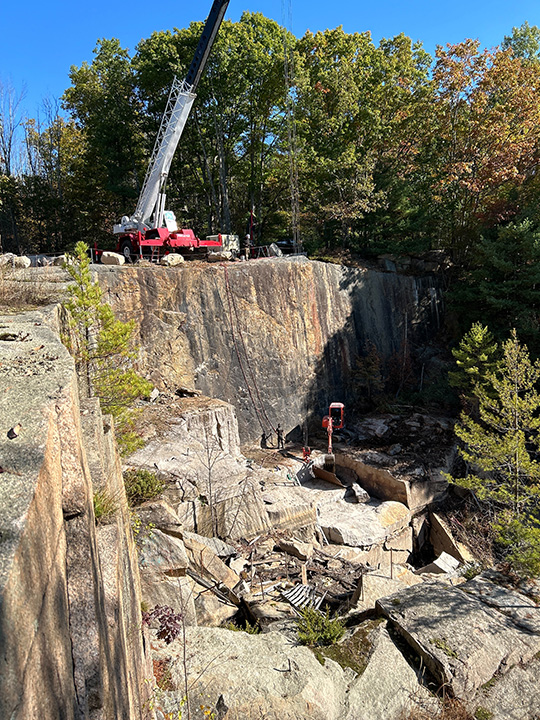
Recreating the size of the aggregate required precision and testing. Samples were extracted, crushed, and screened to match the original granule dimensions, ranging from approximately ½” to 1”. Finished concrete walls are being constructed with meticulous craftsmanship, ensuring no visible formwork joints, embedded items, cracking, surface voids, sand pockets, exposed coarse aggregate, rock pockets, discoloration, or staining. Inspections and quality assurance also play a central role throughout the project. Before full-scale construction of the walls began, numerous mockups were created to test concrete pouring methods, aggregate consistency, wall texture, sandblasting techniques, mix performance, and visual appearance.
To match the visual texture of the original walls, each surface undergoes sandblasting—a labor-intensive process requiring craftsmanship and precision. The depth and smoothness of the sandblasting replicate the original walls, which had weathered for decades under environmental exposure. Achieving the correct sandblast depth is particularly difficult. Too shallow, and the aggregate would not be exposed; too deep, and the surface would lose cohesion and create an irregular texture. Technicians experimented with various pressures and patterns to create a smooth blast that mirrored the wall’s original appearance. Given the walls’ role in shaping the visitor experience and framing the sculptures, each sandblasted surface is being reviewed by the Smithsonian Office of Planning, Design, and Construction’s team of preservationists, architects, and construction managers, underscoring the importance of this preservation effort.
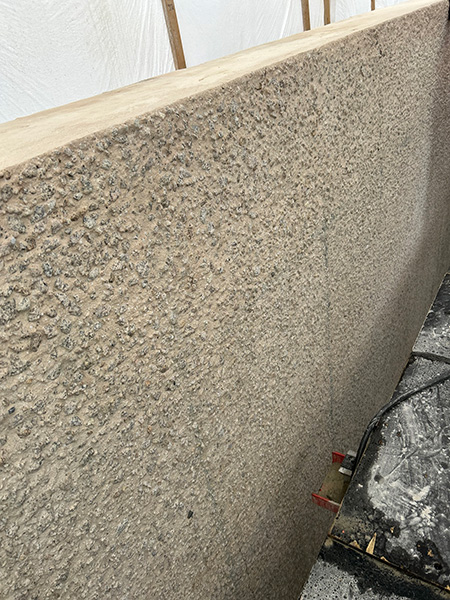
The entire process of rebuilding the walls is an ongoing collaborative effort. From design to execution, it takes dozens of professionals, including preservationists, concrete specialists, masons, engineers, and project managers. To date, more than 83 concrete trucks, yielding over 765 cubic yards of architectural concrete, have been poured—each truckload mixed and batched locally to maintain consistency and reduce environmental impact.
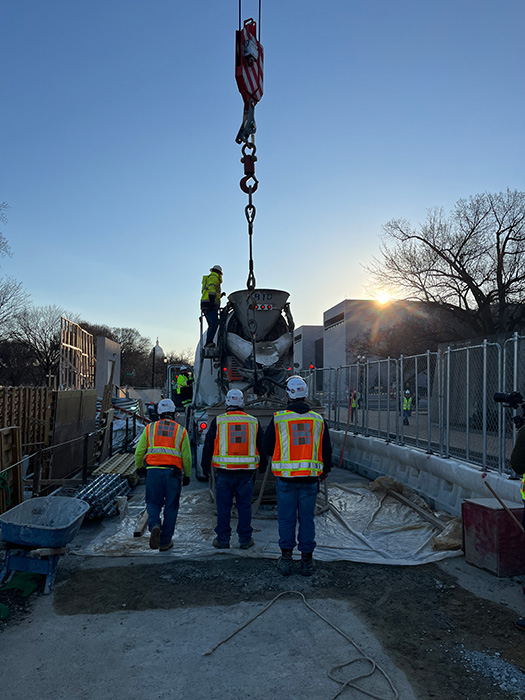
The use of Swenson Pink granite, the careful sandblasting, and the extensive collaborative process highlight the extraordinary effort required to preserve and renew such a culturally significant site. As the Garden reopens with its enhanced design in 2026, the newly constructed walls will stand not just as boundaries, but as enduring monuments to the care, craft, and respect that preserve the historic fabric of the Sculpture Garden. As visitors return to experience the revitalized space, they’ll encounter not only world-class art but also the quiet, powerful presence of craftsmanship that honors the past while embracing the possibilities of the present. These walls, both timeless and newly born, will continue to shape the cultural and visual landscape of the National Mall for generations to come.
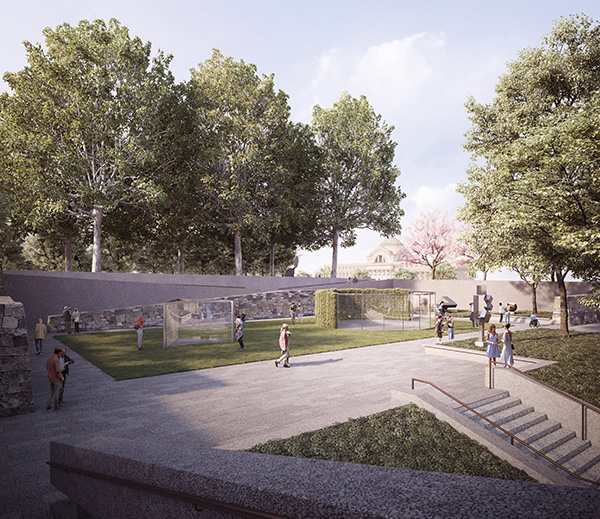